Research and application of drilling fluid environmental protection treatment technology
In the process of oilfield drilling, the total amount of waste is large, the content of pollutants is high, the pollution control of waste is concentrated in the end treatment, the degree of resource utilization is low, the cost is high, the pollution control in the process of drilling can not be realized, and the ecological environment of the oilfield is seriously affected. Aiming at the key technical problems of environmental protection in the drilling process, with the goal of “reduction, harmless and resource utilization”, Xi ‘an Kosun has carried out theoretical research, equipment research and development, technical research and integrated application, and conquered the core technologies of the reduction of drilling waste during drilling and the harmless treatment and resource utilization of drilling waste at the end. The environmental treatment technology of drilling fluid has been applied on a large scale in oil drilling areas at home and abroad.
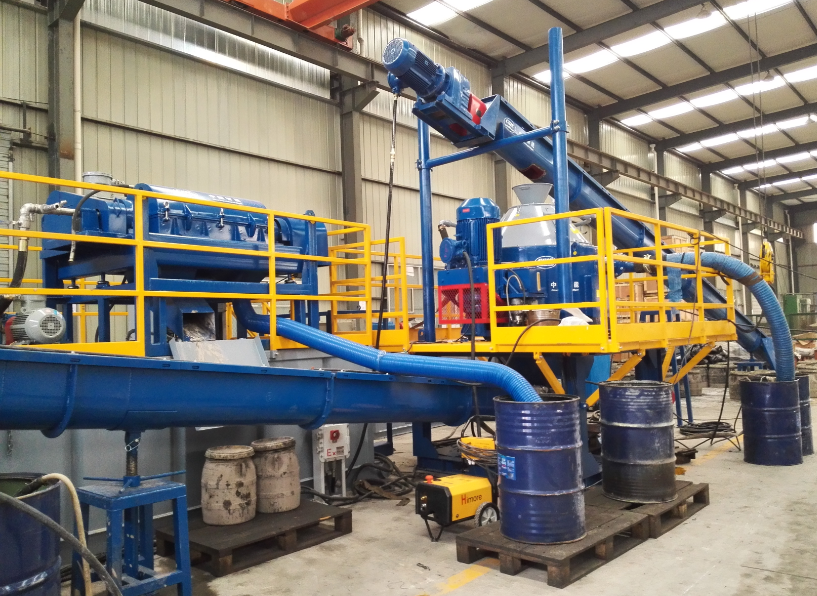
Preliminary separation of solid and liquid
The initial separation of solid and liquid is a process in which the liquid phase after initial separation by solid control equipment (vibrating screen, desilter, desilter and centrifuge) on the drilling site enters the drilling fluid tank for recycling, and the solid phase is transmitted by spiral conveyor to the sand desilter for primary deoiling and then enters the cuttings cleaning and drying machine for separation and discharge of cuttings up to the standard.
The tank is equipped with a mixer, dosing funnel, and pump. After the solid phase enters the sand deoiling tank, turn on the mixer, and add an appropriate amount of water and drugs that can separate the oil and water, so that the oil substances mixed in the solid phase are initially separated and floating on the surface of the mixture, and then use the pump to pump the oil substances away to achieve the first stage separation of the oil substances, and finally stir the solid-liquid mixture in the lower part of the tank and pump it into the cuttings cleaning and drying machine.
The cuttings cleaning and drying machine is equipped with a high-pressure water washing system and rotary dehydration system. While the high-pressure water washing system flushes the cuttings, the rotary dehydration system rotates at high speed, and the mixture realizes the separation of cuttings and drilling fluid sewage under the action of centrifugal force. If the separated cuttings meet the national standard “Comprehensive Sewage Discharge Standard” (GB 8978-2002) level 1 discharge standard, they will be transported from the well site or used for other purposes, otherwise continue to clean until they meet the requirements of the discharge standard; The separated sludge and drilling fluid water enter the sewage storage tank.