With the implementation of new environmental protection laws, the requirements for environmental protection in the oilfield development process are becoming increasingly stringent. Clean production in oilfield operations is a benchmark in the petroleum industry. During the oilfield development process, a large amount of waste mud is the main factor causing environmental pollution and is also one of the high-cost factors in oilfield operations. Therefore, it is important to purify and recycle the mud, which can not only meet environmental benefits but also generate significant economic benefits.
To meet the requirements of mud purification, the petroleum machinery industry has introduced various effective mud purification equipment and systems.
The five-level mud solid control equipment on the oil drilling platform can ensure that the platform meets the requirements for mud treatment under various conditions. The solid control equipment used in mud purification systems operations mainly includes mud circulation tanks, drilling fluid shale shakers, mud cleaners, vacuum degassers, low-speed centrifuges, and high-speed centrifuges.
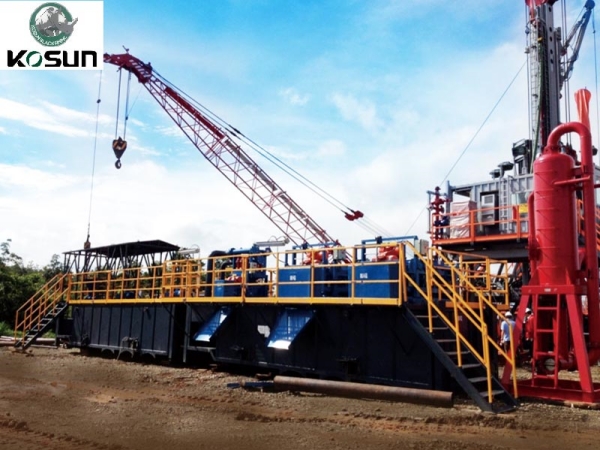
The mud with a large amount of harmful solid phase particles returned from the wellbore flows into the entrance of the first-stage mud purification equipment, the drilling fluid shale shaker, through the wellhead elevated mud trough with a certain slope under the action of gravity. The larger harmful solid phase particles are screened out and discharged by the shale shaker.
When the drilling fluid is invaded by gas, the purified mud obtained through the drilling fluid shale shaker enters the desanding tank of the mud purification tank. By using the suction of the degasser vacuum pump, negative pressure is created in the vacuum tank, allowing the mud to enter the degasser for separation under atmospheric pressure. The separated gas is released at the top of the derrick, and the degassed mud is driven by the rotating impeller of the discharge chamber into the second chamber of the mud purification tank. In the case of gas-free mud, the degasser can be used as a high-power mud agitator to prevent the mud in the mud purification tank from settling.
The purified mud obtained through the drilling fluid shale shaker enters the desanding tank of the mud purification tank. The mud is pressurized and enters the desander of the second-stage solid control equipment, the mud cleaner, through the desanding pump. It is separated again using the cyclone principle to remove harmful solid phase particles with a separation midpoint above 70 microns. The desanded mud is then discharged into the third chamber of the mud purification tank through the overflow pipeline of the desander. According to the overall requirements of the mud purification system, the processing capacity of the desander should exceed 125% of the normal mud circulation volume to ensure sufficient repeated purification of the mud in the purification tank and reduce the sand content in the mud.
The purified mud obtained through the desander is pressurized and enters the desilter of the third-stage purification equipment, the mud cleaner, through the desilting pump. It is separated again using the cyclone principle to remove harmful solid phase particles with a separation midpoint above 36 microns. The desiltered mud is then discharged into the fourth chamber of the mud purification tank through the overflow pipeline of the desilter.
The bottom flows discharged from the desander and desilter contain a certain amount of mud. After the two bottom flows converge, they enter the shale shaker of the combined cleaner for further screening. The recovered mud is returned to the mud tank, while the sand and mud are discharged.
Even after three stages of purification, the mud still contains a large amount of harmful solid phase particles. When the mud is in a non-weighted state, two centrifuges are used in parallel to remove harmful solid phase particles larger than 5 microns. The processed mud is discharged into the fifth chamber of the mud purification tank.
When the mud is in a weighted state, the drilling fluid centrifuge not only removes harmful solid phase particles but also removes the weighting material barite from the mud, resulting in a rapid decrease in mud density and a significant loss of weighting material. To avoid the loss of weighting material and achieve the goal of removing harmful solid phase particles, two centrifuges are used in series, with the medium-speed centrifuge as the first stage and the high-speed centrifuge as the second stage.
The weighted mud extracted from the mud tank by the feed pump of the low-speed centrifuge is processed by the centrifuge, and the processed mud enters the mud purification tank. The bottom flow (containing a large amount of barite) is discharged into the dedicated tank below the medium-speed centrifuge. It is pumped into the second-stage high-speed centrifuge for further separation. The mud containing barite returns to the mud purification tank to maintain the stability of the mud’s performance. The separated harmful solid phase particles are discharged outside the system, achieving the goal of purifying and maintaining the stability of the mud’s performance.
The specific configuration of the solid control equipment at each level will be adjusted according to the specific conditions of the operation site to achieve the best mud purification and recovery effect.
KOSUN- China Solids Control Leader&Drilling Waste Management Expert
Email: sales2@adkosun.com
WhatsApp/Wechat:+86 13379250593
Contact person: Monica Li
Online consulting:
http://www.kosun.com
http://www.kosuneco.com