What are the solid phase control methods for drilling fluids?
To control solid phase in drilling fluid is to remove useless solid phase and retain useful solid phase. There are the following methods:
Ⅰ. Settling Method: This method involves allowing larger solid particles to settle down by circulating the drilling fluid through a large sedimentation tank when it reaches the surface.
Ⅱ. Dilution Method: This method involves adding dispersing media (such as water or oil) to the drilling fluid to reduce the solid phase content. Dispersing agents (such as iron chromates) can also be added to reduce the viscosity of the drilling fluid and improve its ability to carry cuttings.
Ⅲ. Mechanical Equipment Method: This method involves separating solid particles from the drilling fluid using mechanical equipment. This includes vibrating screens, desanders, desilters, centrifuges, and other equipment.
Ⅳ. Chemical Control Method: This method involves adding flocculants to the drilling fluid to increase the aggregation of solid particles, facilitating settling or mechanical removal.
Today, we will mainly introduce the mechanical desanding method. There are various mechanical desanding methods, including vibrating screens, filter presses, vacuum filters, centrifugal filters, centrifugal settling, and cyclone desanders. Due to the relatively high flow rate during core drilling operations and the comparatively low volume of slurry to be treated, cyclone desanders are commonly used. They have desanding capacities several hundred times higher than gravity desanders and can remove particles of around 20 microns. The structural principle of a cyclone desander is shown in the diagram.
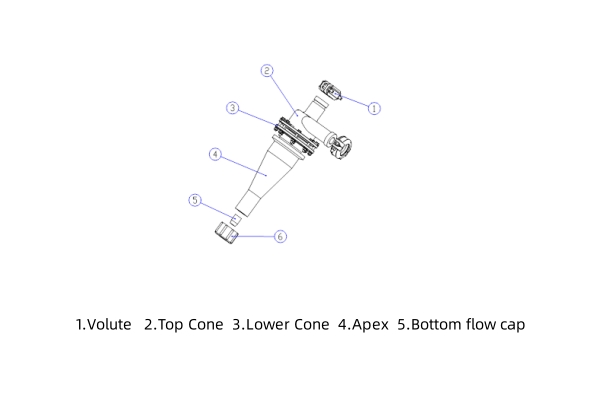
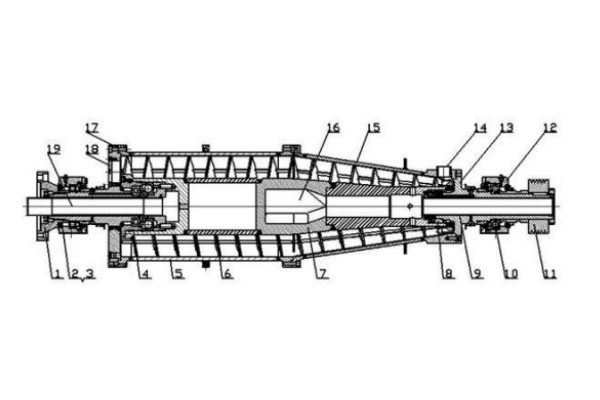
1、Connection joint;2、Big-end bearing pedestal;3、Big-end bearing;4、Big-end inner bearing;5、Cylindrical bowl;6 、Conveyor flight;7、Conveyor mandrel;8、Small-end inner bearing;9、Central tube;10、Small-end bearing;11、Driven wheel of main motor;12、Small-end bearing pedestal;13、Small-end plate;14、Solid outlet;15、Tapered bowl;16、Conveyor outlet;17、Big-end plate;18、Liquid outlet;19、Splined shaft