Trenchless construction is a horizontal drilling project used in construction or infrastructure projects. In the process of trenchless construction, drilling mud is needed to ensure the performance of trenchless drill. To make drilling mud reusable and to reduce drilling costs, contractors often use mud recovery systems to recover drilling mud.
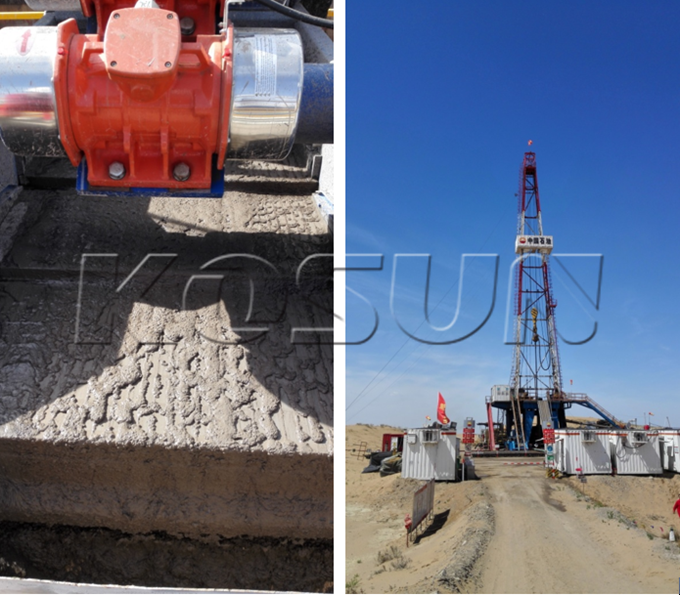
KOSUN has decades of experience in the design and manufacture of mud recovery systems, especially in trenchless projects with a variety of compact mud systems available to customers. According to users’ different requirements and site area limits, KOSUN can provide mud recovery devices with different configurations to meet the requirements of different working conditions. There are usually two types of mud purification systems for trenchless construction: one is the desander swirl purification system and the other is the self-supporting mud recovery system.
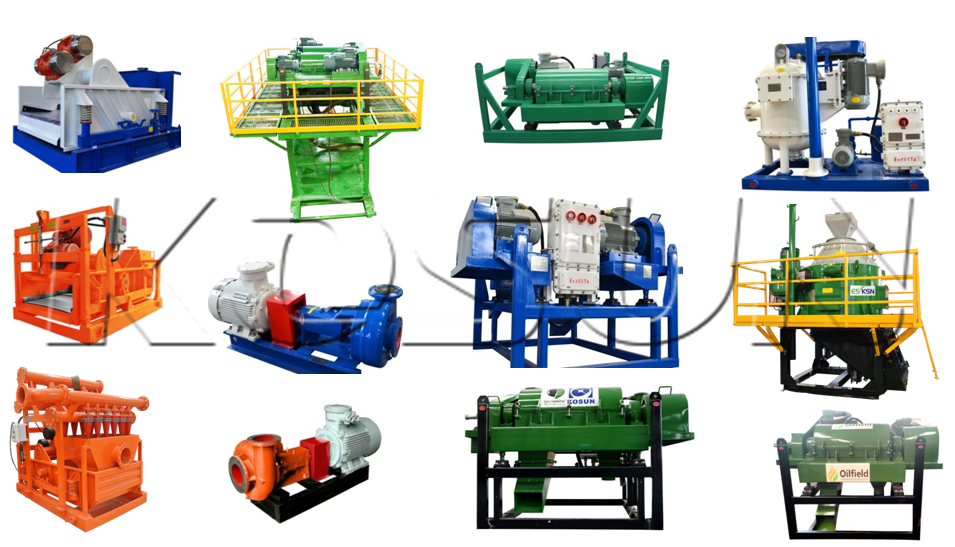
Sand removal swirling purification system covers a small area and is economical. The system is a combination of a cyclone and a shaker, which are mounted on a small collection tank. The desander swirl system is a two-stage separation device, whose function is to remove coarse particles in drilling mud. The desander swirl system is mainly used in engineering that can accept large diameter solid drilling mud, such as piling.
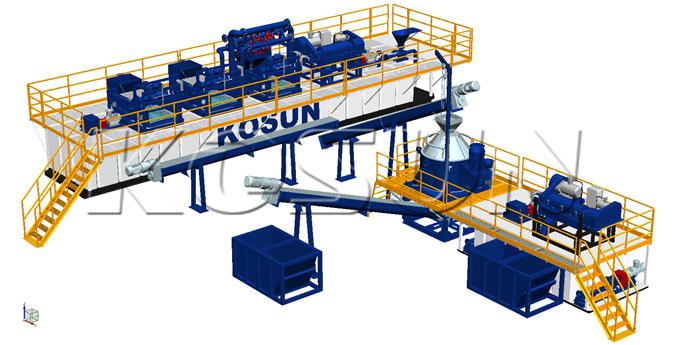
The mud recovery system independently developed by KOSUN can be divided into four separation systems: coarse cuttings separation, sand separation, mud separation and ultrafine solid separation. The higher mud recovery system has a larger mud tank with more room to store purified drilling mud and more crown space for more separation and purification equipment. When the tank surface space is enough, the customer can also choose a centrifuge to reduce the ultra-fine solid phase in the drilling mud, to avoid the enrichment of ultra-fine solid phase in the drilling mud.